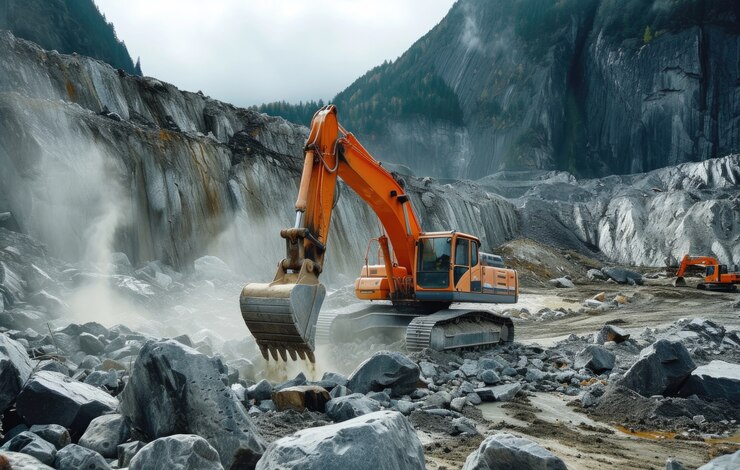
Crushers are indispensable in various industries like mining, construction, and recycling, tasked with reducing large materials into smaller, manageable pieces. Selecting the appropriate crusher is vital for optimizing efficiency, reliability, and cost-effectiveness in your operations. Below is an in-depth exploration of the different types of crushers commonly employed today:
1. Jaw Crushers
Jaw crushers serve as primary crushers, featuring a fixed jaw plate and a movable jaw plate on an eccentric shaft. They excel at breaking down large rocks and ores with high compression strength, making them versatile for a wide range of applications.
2. Impact Crushers
Utilizing impact force, impact crushers are pivotal in quarrying and recycling. They come in two main configurations: horizontal shaft impactors (HSI) and vertical shaft impactors (VSI). HSI crushers use impact energy to crush materials, while VSI crushers employ velocity to break down rocks. These machines are crucial for reducing large materials into smaller, more manageable sizes, supporting efficient material handling and recycling efforts across various industries.
3. Cone Crushers
Cone crushers operate by squeezing material between a mantle and a concave, making them ideal for secondary or tertiary crushing of medium-hard to very hard materials. Their high crushing ratio and reliability make them essential in aggregate and mining applications.
4. Gyratory Crushers
Gyratory crushers use a conical mantle and concave liner arrangement to crush materials. These crushers are commonly used in large-scale mining and ore processing operations due to their robust design and ability to handle very large feed sizes.
5. Roll Crushers
Roll crushers employ two counter-rotating rollers to crush materials by compression. They are suitable for medium-hard to hard materials such as rock and ore, commonly used in mining and construction industries for producing finer-sized products.
6. Hammer Mills
Hammer mills are high-speed rotary crushers equipped with multiple hammers fixed to a central shaft. They are versatile machines capable of crushing a wide range of materials from soft to medium-hard, making them suitable for primary, secondary, or tertiary crushing applications.
Choosing the Right Crusher
Selecting the optimal crusher type depends on several factors, such as material characteristics, the required output size, and operational considerations like maintenance and energy efficiency. Consider the following when making your choice:
- Material Hardness: Assess whether the material is soft, medium-hard, or hard.
- Feed Size: Determine the size of the material entering the crusher.
- Output Size: Specify the desired size of the final product.
- Capacity: Evaluate the required throughput or production rate.
- Operating Costs: Factor in maintenance requirements and energy consumption.
Understanding these factors will help you make an informed decision to maximize productivity and profitability in your crushing operations.
Conclusion
Choosing the right crusher is crucial for optimizing your material processing operations. Whether you’re crushing aggregates, minerals, or recyclables, the right crusher type can significantly impact your operation’s efficiency and overall success. By carefully evaluating your needs and considering factors like material characteristics and output requirements, you can select the crusher that best fits your application, ensuring reliable performance and cost-effective operation.